Influence of conventional finishing on fabric color Post-finishing is the last process of the…
The Working Process of Dyeing Lab
Have you ever stared confused at an ingredient list on a clothing tag wondering what cryptic chemical is used to achieve that vibrant red?
Or scoured the labels trying to figure out why some tees retain their color season after season while others fade to pale remnants after a few washes?
Well, I’m about to decode the secrets clothing makers use to work their color magic so they withstand the test of time.
In this article, we infiltrate the hidden world inside textile dyeing laboratories where shades are born before they hit retail stores.
I’ll be your top-secret guide into this obscure, high-security facility few outsiders ever witness first-hand, especially the working process of dyeing labs.
We’ll uncover complex industrial techniques even insider chemists find bewildering like spectral fingerprinting, computer predictive modeling, and ingenious chemical tweaks that trick fibers into absorbing more color than should be possible!
So let’s sneak a peak into the color science transforming textile manufacturing as we know it!
This shadowy field could redefine fashion as fundamentally as the loom and spinning wheel did in their era.
Table of Contents
- Chapter 1: Critical Role of a Dyeing Facility
- Chapter 2: Key Areas and Equipment in a Dyeing Lab
- Chapter 3: Step-by-Step Workflow in a Dyeing Lab
- Chapter 4: Expert Technique – Judicious Dye Selection
- Polyester Dyeing Scenario
- Wool Dyeing Situation
- Chapter 5: Computer Color Matching System
- Step 1: Data Acquisition
- Step 2: Prediction Logic
- Step 3: Lab Trial
- Step 4: Result Comparison
- Step 5: Iteration or Batch Release
- CCM Benefits
- The Future of Textile Dyeing Labs
- Artificial Intelligence
- Automation
- Augmented Reality
Chapter 1: Critical Role of a Dyeing Facility
While apparel design studios and fashion runways bask in the spotlight, few recognize the silent partner that transforms their imaginative creations into wearable reality. Yes, I’m referring to the dyeing facility which specialty colors yards of fabric based on a designer’s vision.
Let’s briefly touch upon 5 key roles played by a textile dyeing lab:
Optimizing Dye Use
Carefully engineering the optimum combination of dyes, chemicals, and auxiliaries for reproducing a color with minimal processing costs
Upscaling New Shade Recipes
Taking a lab color recipe and adapting practices to seamlessly transfer onto factory floor bulk machinery
Ensuring Consistent Quality
Implementing process controls and testing protocols so that production runs deliver uniform coloring meeting all specifications
Validating Eco Compliance
Testing and certifying that colorant chemistry and effluents meet stringent quality, safety, and environmental norms
Building Process Knowledge
Accumulating technical knowhow on dye selection, application procedures, and issue resolution for continuous improvement net
As you can see, a dyeing facility is the bridge between inspiration and production. Balancing creativity on one end and quality compliance on the other involves considerable behind-the-scenes effort.
Now that we know why dyeing labs matter, let’s get into specifics of their workspace and tools of the trade!
Chapter 2: Key Areas and Equipment in a Dyeing Lab
A large dyeing facility comprises multiple specialized zones such as:
Incoming Material Inspection
Here, suppliers’ deliveries of fabrics and dyes undergo tests to ensure they meet trade quality standards related to composition, strength, color, etc.
Computer Color Matching
The heart of the facility contains software tools, spectrophotometers, and scientific techniques for predicting dye mixes to match color targets and tolerance checks after trials.
Wet Processing Hall
Where substrate preparation, continuous fabric dyeing at longer lengths, and post-treatment happen with the aid of specialized high-production machinery to mimic factory environments.
Sample Dyeing Room
Smaller instruments that handle yarn, fabric swatches, and tests related to lab dip color matching, fastness properties evaluation, and physical and chemical testing. Among the diverse equipment found here, let me call out some interesting ones:
GYROWASH – a high-speed instrument that performs wash, rinse, and drying cycles on fabric specimens as per apparel/home laundering conditions
CROCKMETER – employs a rubbing action on dyed fabrics to assess the potential for color loss during everyday friction/abrasion
SPECTRA LIGHT BOOTH – contains special lights spanning the solar spectrum for color matching with illumination representing consumer usage
INKJET PRINTER – directly prints dye or pigment-based colors onto substrate offering flexibility of design compared to conventional dyeing
GSM CUTTER – accurately cuts fabric swatches of specified area for determining key properties like grams per square meter or ends per inch
Now that we know the landscape and tools, we’re ready to immerse in the actual dyeing workflow. Let’s get our hands dirty!
Chapter 3: Step-by-Step Workflow in a Dyeing Lab
Each assignment in the lab flows through a sequential procedure personalized to the customer’s needs:
Step 1 – Substrate Analysis
Incoming fabric properties like fiber type (wool, cotton, polyester, etc), yarn thickness, construction style (knitted, woven, non-woven), weight, weave pattern, and pre-treatment are assessed.
Step 2 – Dye Selection
Based on substrate and fastness expectations (crocking, light exposure, etc), the appropriate dye type and application class is chosen – sulfur, azoic, reactive, disperse, cationic, etc.
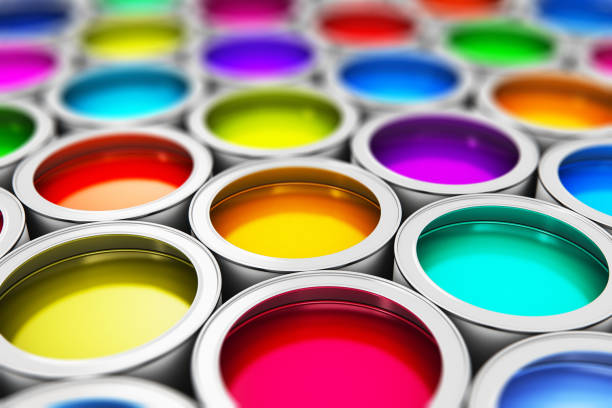
Step 3 – Recipe Prediction
A small fabric swatch is analyzed using spectral data and sensor techniques to generate a putative dye/chemical formula for achieving the same color.
Step 4: Lab Trial
The computer-suggested recipe is manually prepared, applied on the substrate via a suitable dyeing machine, and assessed after post-treatment through visual examination and instrument verification.
Step 5 – Batch Creation
If the lab trial clears all quality checks, bulk quantities of selected dyes, auxiliaries, and substrates are weighed/set up on factory floor machinery for larger production.
Step 6 – Continual Monitoring
During extended runs, parameters like liquor temperature, pH, flow rate, mechanical agitation, etc are monitored to minimize color variation across thousands of meters.
As evident, transitioning a color inspiration into a consistently reproducible reality involves considerable science and artisanship. Both human expertise and automation combine for a results synthesis that balances creativity with compliance.
Now that you know the method, let me share a real-world dye selection scenario our colorists handle.
Chapter 4: Expert Technique – Judicious Dye Selection
While common perception associates dyeing with creativity, considerable logical thinking goes into choosing the right colorant type. Let me illustrate with two examples:
Polyester Dyeing Scenario
For coloring polyester fabrics, dispersed dyes get selected due to polarized structure enabling desired migration and bonding. Comparatively, reactive or sulfur dyes lack substantive power leading to unsatisfactory shade depth despite higher application concentrations.
Wool Dyeing Situation
The isotropic wool fiber matrix allows both acidic and reactive dye classes to deliver vibrant colors. But factors like lightfastness, penetration kinetics and batch-to-batch reproducibility make acid dyes the prudent primer choice before considering next-gen variants.
I share these real-world dye selection stories to highlight that while the end objectives of a textile technologist and fashion designer converge, the underlying thought process differs significantly.
Imagination guides initial creation whereas scientific rigor transforms those nascent ideas into practicality!
Let me give you a peek into an even more intricate procedure – computer color matching.
Chapter 5: Computer Color Matching System
Among recent advancements that enhanced precision, automation, and objectivity, computer color matching (CCM) systems stand tall. The high-tech color measurement and formulation techniques not only improve reproducibility but also eliminate human errors and subjective bias that inevitably creep in during visual color matching.
But how does CCM work? Let’s dive deeper.
The core principle lies in quantifying colors based on their unique visible light reflectance signature or fingerprint. It comprises these key steps:
Step 1: Data Acquisition
The spectrophotometer captures the spectral reflectance curve of the fabric swatch target color and converts light signals into digital readings across wavelength bands.
Step 2: Prediction Logic
Complex software models containing calibration data on dye absorption behavior calculate a putative recipe that theoretically matches standard sample readings when combined.
Step 3: Lab Trial
The computer-suggested formulations are physically dyed on specified material at pilot scale for creating the test color sample.
Step 4: Result Comparison
Reflectance data of lab-dyed and original standard fabric are statistically analyzed with permissible ΔE divergence.
Step 5: Iteration or Batch Release
If the difference metric exceeds the cut-off, the recipe gets further optimized. For confirmation batches, bulk production gets approved.
While seemingly straightforward, considerable mathematics, physics, and chemistry manifest delivering this digital mimicry.
Let’s look at an example highlighting its benefits.
CCM Benefits
Shifting from manual color matching to a CCM system for evaluating polyester lab dips yields some insightful outcomes:
– Objective repeatability improved as human biases were eliminated
– Enhanced color differentiation led to matching shades earlier deemed impossible
– 15-20% savings in dyestuff and auxiliaries translated into a better environmental footprint
The merits of scientific pigmentation shine through here! With CCM adoption expanding, I foresee dyeing labs transforming from experience-driven facilities to data-powered think tanks shortly!
The Future of Textile Dyeing Labs
We covered tremendous ground unpacking the workings of modern textile dyeing laboratories. Before we sign off, here is my projection on upcoming technologies and trends likely to reshape this color-critical industry:
Artificial Intelligence
AI-based cognitive models will take the baton from existing CCM systems reaching new heights in predictive accuracy.
Automation
Human-free robotic dye selection, preparation, dispensing, and quality testing will manifest through advanced AI and mechanical engineering working in tandem.
Augmented Reality
AR tools enabling real-time remote color collaboration between designers, dyeing technicians, and factory personnel will emerge as the new normal.
I can envisage these innovations enabling customization, hyper-flexibility, and democratization at a scale unimaginable in today’s ecosystem.
If you found this behind-the-scenes dyeing lab expedition insightful, stay tuned for more as I track exciting developments from the cutting edge of textile science innovation. Until next time, take care!