Clothing comfort balances body heat and moisture in various environments and activities. It achieves balance.…
Exploring the Seventeen Core Properties of Textile Fibers
The properties of textile fibers refer to the physical, chemical, and structural properties of fiber materials. These attributes influence the processing, weaving, dyeing, finishing, and ultimate performance and applications of fibers. From strength to softness, from moisture absorption to flame resistance, fibers exhibit a diverse range of properties, each playing a crucial role. In this article, we will delve into the seventeen key characteristics of textile fibers, taking you on a journey to explore this fascinating field and adding a touch of vibrancy to your world of fibers!
Table of Contents
Abrasion resistance
Abrasion resistance refers to the ability to resist wear and tear from friction during wear, contributing to the durability of fabrics. Garments made from fibers with high tensile strength and good abrasion resistance can withstand prolonged wear, showing signs of wear and tear only after an extended period.
Nylon is widely used in sportswear, such as ski jackets and football jerseys, due to its exceptional strength and abrasion resistance. On the other hand, acetate fiber, known for its excellent draping properties and low cost, is often used as lining material in outerwear and jackets.
However, due to the poor abrasion resistance of acetate fiber, the lining may wear out or develop holes before the corresponding abrasion appears on the outer fabric of jackets.
Water absorbency
Water absorbency refers to the ability to absorb moisture, often measured by the regain rate. The water absorbency of fibers refers to the percentage of moisture absorbed by dry fibers under standard conditions of 70°F (equivalent to 21°C) and 65% relative humidity.
Hydrophilic fibers, which readily absorb water, include all natural fibers from animals and plants, as well as two types of synthetic fibers: viscose rayon and acetate. Hydrophobic fibers, on the other hand, have difficulty absorbing water or can only absorb minimal amounts. Except for viscose rayon, Lyocell fibers, and acetate, all other synthetic fibers are hydrophobic. Glass fibers, do not absorb water, while other fibers typically have a regain rate of only 4% or lower.
The water absorbency of fibers affects various aspects of their applications, including:
- Skin comfort: Poor water absorbency can lead to a sensation of cold and dampness due to sweat accumulation.
- Static electricity: Hydrophobic fibers can accumulate static electricity, leading to problems such as clothes clinging and sparking. Dust particles are also attracted to the fibers due to static electricity.
- Size stability after washing: Hydrophobic fibers tend to shrink less than hydrophilic fibers after washing, as they absorb minimal water and expand less, contributing to fabric shrinkage.
- Stain removal: Stains are easier to remove from hydrophilic fibers because they absorb cleaning agents and water more readily.
- Water repellency: Hydrophilic fibers often require more durable water-repellent treatments, as these chemical treatments enhance their water repellency.
- Wrinkle recovery: Hydrophobic fibers generally have better wrinkle recovery, especially after washing and ironing, as they do not absorb water, expand less, and dry in a wrinkled state.
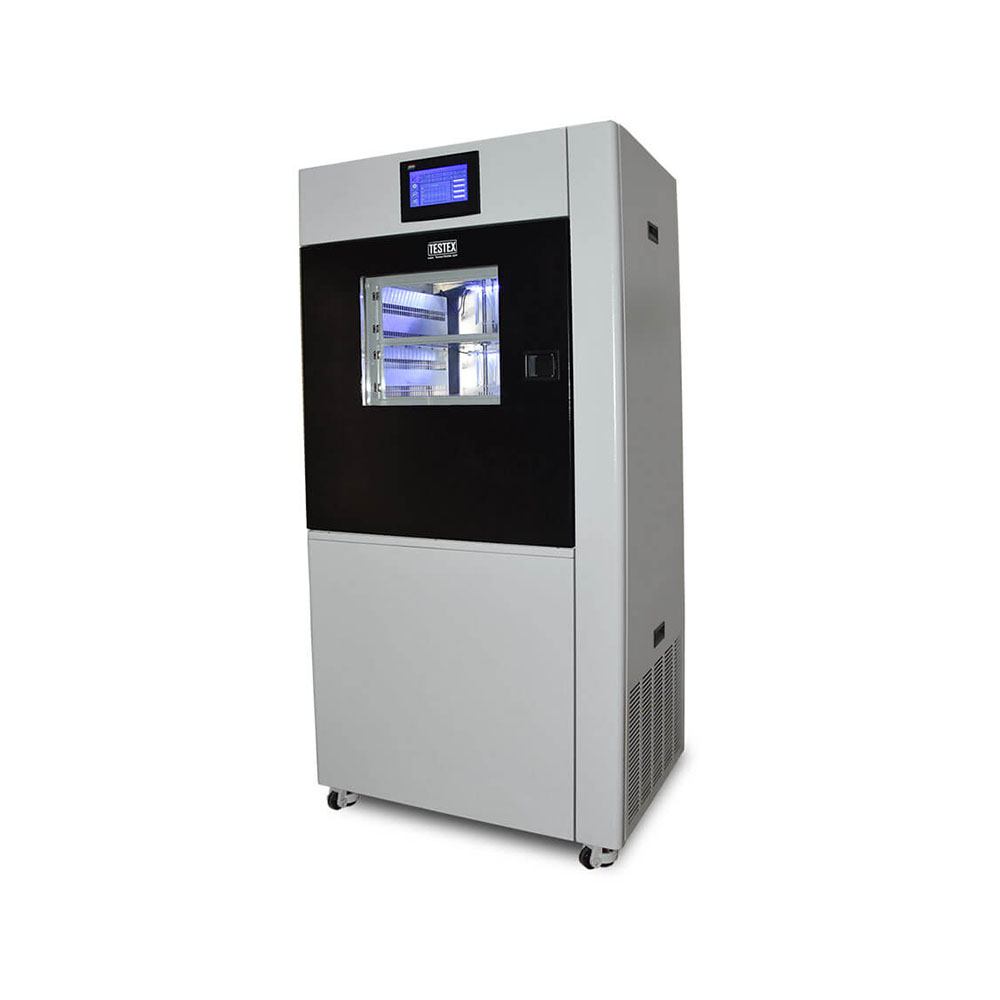
Chemical Interaction
In textile processing, such as printing, dyeing, and finishing, as well as in household or professional care and cleaning processes involving the use of soaps, bleaching agents, and dry cleaning solvents, fibers typically come into contact with chemicals. The type of chemicals, their strength, and the duration of exposure determine the extent of their impact on fibers. Understanding the effects of chemicals on different fibers is crucial, as it directly relates to the care required during cleaning.
Fibers react differently to chemicals. For example, cotton fibers have relatively low resistance to acids but exhibit good resistance to alkalis. Additionally, cotton fabrics may experience some loss of strength after undergoing chemical resin wrinkle-free finishing.
Coverage
Coverage refers to the ability to fill a certain area. Textiles made from coarse fibers or curled fibers provide better coverage compared to fine, straight fibers. These fabrics are warm, have a full hand feel, and require fewer fibers to weave.
Wool is widely used in winter clothing due to its excellent coverage provided by its curls, which trap a significant amount of still air within the fabric, insulating it against external cold air. The effectiveness of fiber coverage depends on its cross-sectional shape, longitudinal structure, and weight.
Elasticity
Elasticity refers to the ability to elongate when subjected to tension (stretch) and return to its original state when the external force is removed (recovery). The elongation of fibers or fabrics under external forces can make garments more comfortable to wear, and the resulting seamstress is relatively small.
There is also a trend towards increased tensile strength. Complete recovery can help prevent garments from sagging at elbows or knees, thus avoiding relaxed deformation. Fibers that can elongate at least 100% are called elastic fibers. Spandex fibers (also known as Lycra or elastane) and rubber fibers belong to this category. After elongation, these elastic fibers can almost forcefully return to their original length.
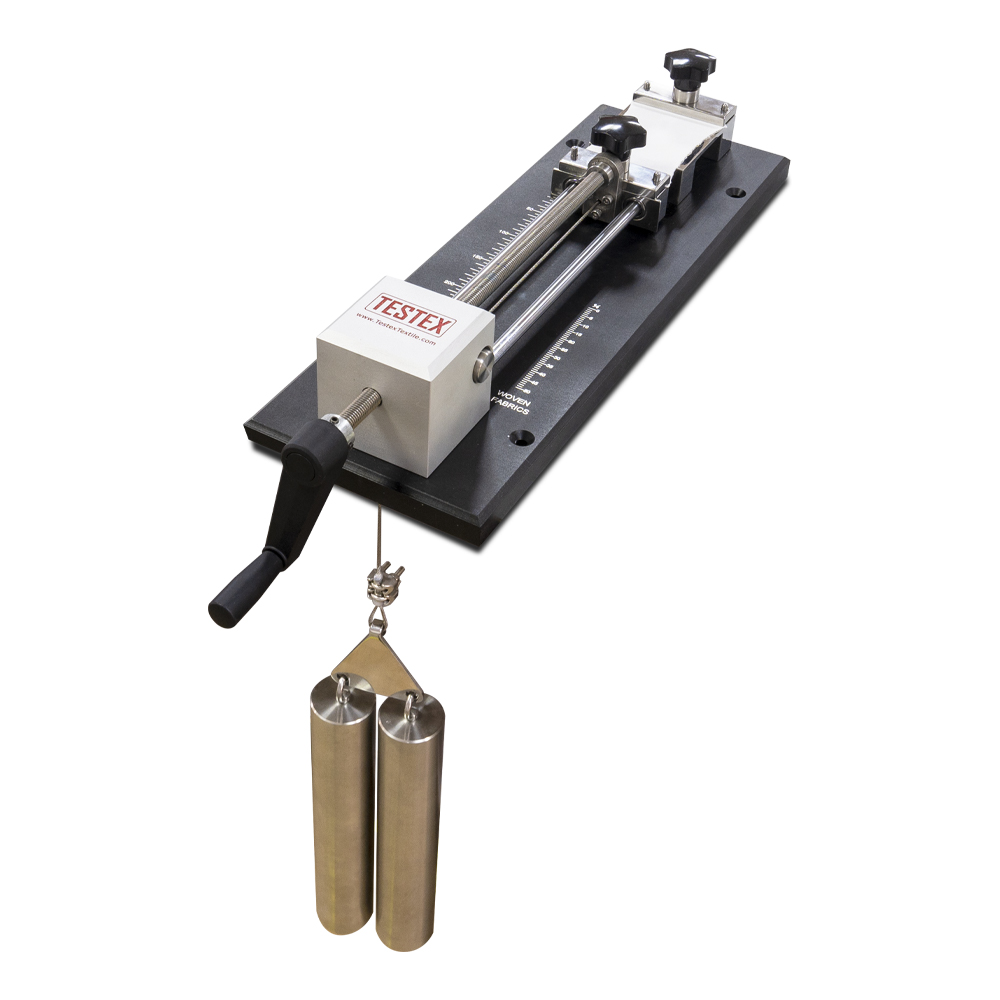
Environmental conditions
Environmental conditions have varying effects on fibers, and how fibers and the final fabrics react to exposure, storage, etc., is crucial.
Here are some examples:
- Wool garments need protection against moth damage during storage, as they are susceptible to moth infestation.
- Nylon and silk, when exposed to sunlight for extended periods, experience decreased strength, making them unsuitable for use in curtains and door/window coverings.
- Cotton fibers are prone to mold growth, so they should not be stored for long periods in damp environments.
Flammability
Flammability refers to the ability of a material to ignite or burn. This is an important characteristic as people’s lives are often surrounded by various textiles. We know that clothing or indoor furniture, due to their flammability, can cause serious harm to consumers and result in significant material losses.
Fibers are generally classified as highly flammable, non-flammable, or flame-retardant:
- Highly flammable fibers are easily ignited and continue to burn.
- Non-flammable fibers have relatively high ignition points, burn slowly, and self-extinguish after the ignition source is removed.
- Flame-retardant fibers do not burn.
Highly flammable fibers can be transformed into flame-retardant fibers through finishing processes or by altering fiber parameters. For example, conventional polyester is highly flammable, but Trevira polyester, after treatment, exhibits flame-retardant properties.
Softness
Softness refers to the property of fibers being able to bend repeatedly without breaking. Soft fibers, such as acetate fibers, can be used to produce fabrics and clothing with good drapes. On the other hand, rigid fibers like glass fibers cannot be used in clothing production but can be utilized in decorative fabrics that require a relatively stiff hand. Generally, the finer the fiber, the better the drape. Softness also influences the hand feel of the fabric.
While fabrics with good drapes are often desired, there are occasions when stiffer fabrics are needed. For example, in garments with capes (clothes hanging from the shoulders and flowing outward), stiffer fabrics are used to achieve the desired shape.
Hand feel
Hand feel refers to the sensation felt when touching fibers, yarns, or fabrics. The hand feel of a fiber is influenced by its shape, surface characteristics, and structure. Fibers come in various shapes, such as round, flat, or multi-lobed. They also have different surface textures, such as smooth, serrated, or scaled.
Fibers are either curly or straight in shape. Yarn type, fabric structure, and finishing processes also affect the hand feel of the fabric. Terms commonly used to describe fabric hand feel include soft, smooth, dry, silky, stiff, coarse, or rough.
Gloss
Gloss refers to the reflection of light from the surface of fibers. Different characteristics of fibers influence their glossiness. Surfaces with gloss, fewer bends, flat cross-sectional shapes, and longer fiber lengths enhance light reflection. The stretching process during fiber manufacturing increases gloss by smoothing the surface. Adding matting agents disrupts light reflection, reducing gloss.
The gloss of fabrics is also influenced by yarn type, weave, and all finishing processes. The requirements for gloss depend on fashion trends and customer needs.
Pilling
Pilling refers to the formation of small, tangled fiber balls on the surface of a fabric. These balls are made up of short, broken fibers that intertwine with each other. Pilling typically occurs when the fiber ends break off from the fabric surface, often caused by wear. Pilling is undesirable as it makes fabrics, such as bed sheets, look old and unsightly, and can feel uncomfortable. Pilling occurs in areas of frequent friction, such as collars, underarms, and sleeve cuffs.
Hydrophobic fibers are more prone to pilling than hydrophilic fibers because hydrophobic fibers are more likely to attract static electricity and are less likely to shed from the fabric surface. Pilling is rarely seen on 100% pure cotton shirts, but it is very common on polyester-cotton blend shirts worn for some time. While wool has hydrophilic properties, pilling occurs due to its scaly surface. Fibers twist and tangle with each other, forming a pill. Strong fibers are more likely to grip onto fabric surface pills. Low-strength fibers that are prone to breakage are less likely to pill due to the easy shedding of pills.
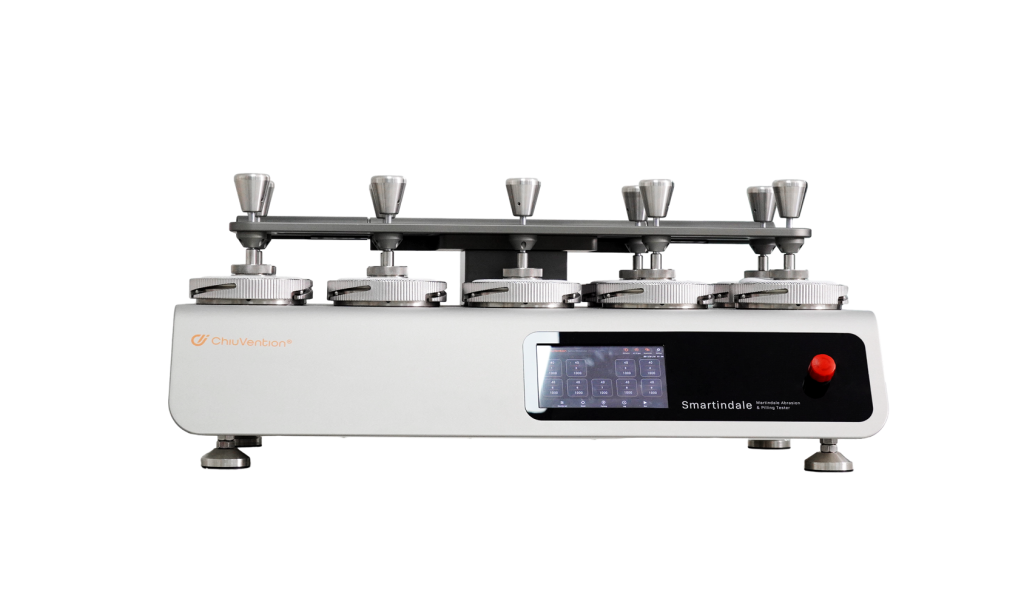
Resilience
Resilience refers to the ability of a material to elastically recover its shape after being folded, twisted, or distorted. It is closely related to wrinkle recovery ability. Fabrics with good resilience are less prone to wrinkling, thus maintaining their appearance well.
Coarser fibers have better resilience because they have greater mass to absorb strain. Additionally, the shape of the fiber also influences its resilience, with round fibers having better resilience than flat fibers.
The nature of the fiber is also a factor. Polyester fibers have outstanding resilience, while cotton fibers have poor resilience. Therefore, these two fibers are often blended in products such as men’s shirts, loose-fitting tops, and bed sheets, which is not surprising.
However, fibers with good resilience can be a bit problematic when forming distinct wrinkles on clothing. It is easy to form creases on cotton fabrics or coarse synthetic fabrics, but not so much on dry wool fabrics. Wool fibers are resistant to bending and wrinkling, and they can straighten out again afterward.
Relative density
Relative density refers to the ratio of the mass of fibers to the mass of an equal volume of water at 4°C. Light fibers can create fabrics that are warm yet not bulky, resulting in thick, fluffy fabrics that still remain a relatively lightweight. Acrylic fiber is the best example, as it is much lighter than wool but possesses similar properties, making it widely used in lightweight and warm blankets, scarves, thick socks, and other winter items.
Static electricity
Static electricity is the result of friction between two different materials, leading to the generation of electric charges. When these charges accumulate on the surface of fabrics, clothing may cling to the wearer’s body or lint may adhere to the fabric. Contact between the fabric surface and another object can result in static sparks or shocks, which is a rapid discharge process. Static electricity phenomenon can be eliminated when the charge is transferred at the same speed as it is generated on the fiber surface.
Moisture contained within the fibers acts as a conductor to dissipate charges and prevent the aforementioned static electricity effects. Hydrophobic fibers, on the other hand, tend to generate static electricity due to their low moisture content. Static electricity can also occur in natural fibers, but only when the environment is very dry, similar to hydrophobic fibers. Glass fibers are an exception among hydrophobic fibers because static charges cannot accumulate on their surfaces due to their chemical composition.
Fabrics containing electrobic fibers (fibers capable of conducting electricity) do not suffer from static electricity issues, as the carbon or metal content allows the fibers to transfer accumulated static charges. Due to common static electricity problems on carpets, materials like Monsanto Ultron nylon, which contains electrobic fibers, are used. Electrobic fibers eliminate shocks, fabric clinging, and dust adhesion. Using low-static fibers in environments where static electricity poses a risk, such as hospitals, near computers, or areas with flammable or explosive liquids or gases, is crucial for safety.
Strength
Strength refers to the ability of a fiber to resist stress. Fiber strength refers to the ability of a fiber to resist breaking under tension or stress. It is a crucial characteristic as it determines the durability and performance of textiles made from the fiber. Fiber strength is typically measured in units such as grams per denier (g/d) or Newtons per tex (N/tex), indicating the force required to break a single fiber of a certain length and thickness. Higher fiber strength indicates greater resistance to breaking and stretching, making the material more suitable for various applications, including apparel, industrial textiles, and composite materials.
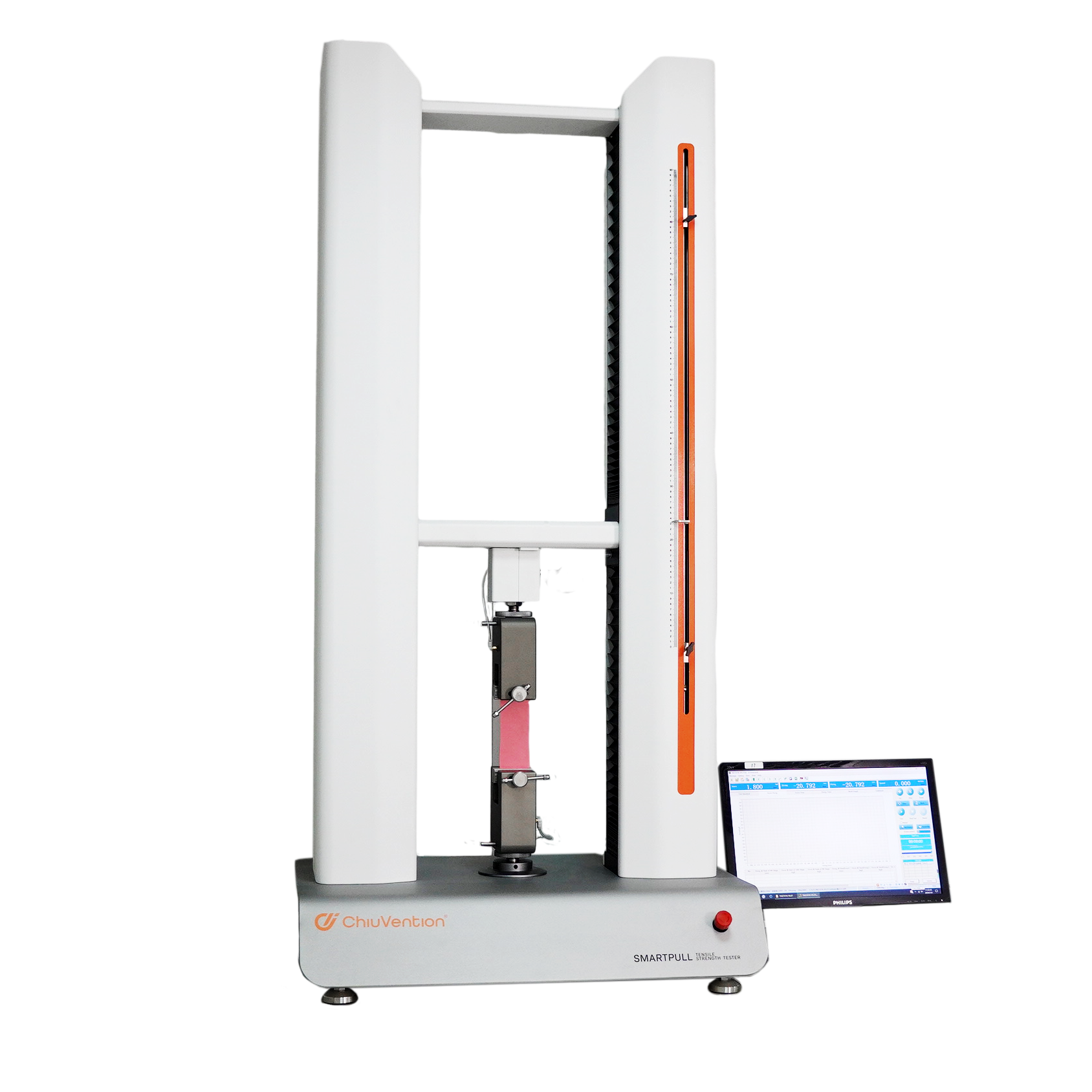
Thermal plasticity
Thermal plasticity refers to a fiber’s ability to withstand heat, which is a crucial factor affecting its application performance. Typically, this is an important consideration in fiber processing, as fibers often undergo heating during various textile processes such as dyeing, ironing, and heat setting. Additionally, heat is frequently used for caring and refreshing garments and indoor furnishings.
Some thermal effects are temporary and reversible, occurring only during the application of heat. For instance, in dyeing, fiber properties may temporarily change during heat application but return to normal upon cooling. However, some thermal effects can be permanent, as heat can cause molecular rearrangement leading to fiber degradation. In contrast, heat setting alters molecular arrangement to make the fabric more stable (with minimal shrinkage) and wrinkle-resistant, without significant degradation. However, prolonged exposure to high temperatures can lead to degradation, including reduced strength, fiber shrinkage, and discoloration. Many consumers have experienced severe degradation or even damage to their clothing from excessive ironing at high temperatures.
During heating, thermoplastic fibers soften and can melt into a liquid state at higher temperatures. Many synthetic fibers exhibit thermoplasticity. By heating fabrics containing thermoplastic fibers, creases and folds can be formed without melting the fibers. These creases and folds become permanent once the temperature decreases. When heated (softened), thermoplastic fibers can be molded, and once cooled, the molded shape is retained (care must be taken when ironing garments made of synthetic fibers to avoid softening or melting, which can cause the fabric to stick to the iron). This method can also be used to shape garments, providing excellent dimensional stability for thermoplastic fabrics.
Core absorption
Core absorption refers to the ability of fibers to transfer moisture from one place to another. Typically, moisture travels along the surface of fibers, but it can also pass through fibers when liquids are absorbed. The tendency for core absorption often depends on the chemical and physical composition of the outer surface of the fiber. A smooth surface reduces core absorption.
Certain fibers, such as cotton, are hydrophilic fibers and have good core absorption. Other fibers, such as olefins, are hydrophobic fibers, but they can exhibit good core absorption when they have a very low denier (i.e., very fine fibers). This property is particularly important for garments like workout clothes and running gear. Sweat expelled by the body is transferred along the surface of the fibers through core absorption to the outer surface of the garment, where it evaporates into the air, providing better comfort.
In conclusion, the properties of textile fibers shape their performance and applications significantly. From abrasion resistance to thermal plasticity, each characteristic plays a crucial role. By understanding these traits, we can make informed choices in textile selection. Fibers enrich our lives in diverse ways, from crafting durable gear to luxurious apparel. Let’s celebrate the vibrancy they add to our world!